How To Predict Die Swell in Rubber Compounds using a Premier® RPA
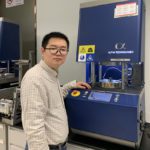
Author
Li Wan
Application Engineer, China
Does This Die Make Me Look Bloated?
Rubber compounds are viscoelastic materials that are subject to die swell (also called the Barus Effect) and dimensional stability issues when processed by extruding or calendaring in the factory. Die swell is a phenomenon that occurs when the extruded rubber compound leaves the extruder die with a greater dimensional diameter than the diameter of the extruder die orifice itself. This effect is demonstrated In Figure 1 below.

Figure 1 Extruding rubber through a die orifice
For many years, efforts have been made to predict compound die swell in extrusion. The most common method for measuring die swell and other rheologic behavior is by using a capillary rheometer. A capillary rheometer such as the ARC 2020 can provide accurate data, however the complicated testing process it requires limits its wide use. Fortunately, the Premier RPA is unique in its ability to perform tests under a range of large strain/ frequency combinations. More importantly, it has the great advantage of being easy to operate while delivering excellent repeatability. In short, the Premier RPA is a more convenient way to predict the die swell.
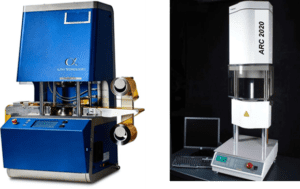
Figure 2. The Premier RPA and ARC2020 Capillary Rheometer
Your results may vary. Well… actually no, they won’t.
To demonstrate the ability of the Premier RPA to predict die swell, we compared testing results between the RPA and an ARC 2020. As can be seen in Figure 3 below, RPA uncured tan δ inversely correlates to the capillary rheometer running adie swell test. Using simple correlation methodology, RPA Tan δ at appropriate (usually high) strain correlated well with the die swell data from the capillary rheometer. Specifically, the trend is increasing Tan δ when die swell is reduced (lower intrinsic elasticity).
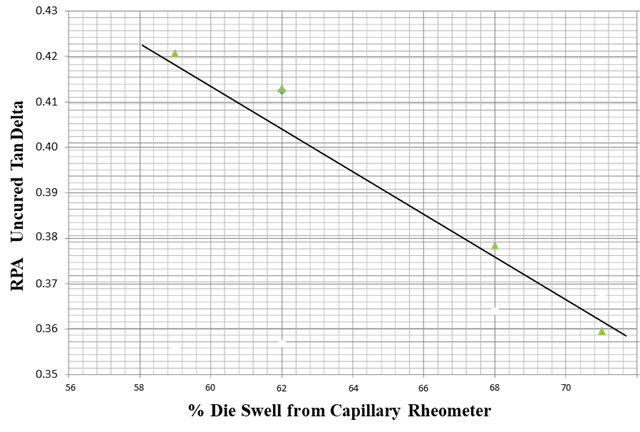
Figure 3 Die Swell from capillary rheometer, RPA Tan Delta vs. phr Silica
One minor issue is that to achieve the best prediction of die swell with the RPA requires adjustments in the applied strain during frequency sweeps to simulate more effectively the destruction of the filler network which is also happening in the factory during an extrusion operation, especially for fully reinforcing fillers. When you setup the test, the specific strain amplitude applied during the performance of the RPA frequency sweep is very important, and actual process conditions, screw speed and temperature, head temperature etc, can also be considered as important reference parameters.
This is covered more completely in Part 2 of this blog.
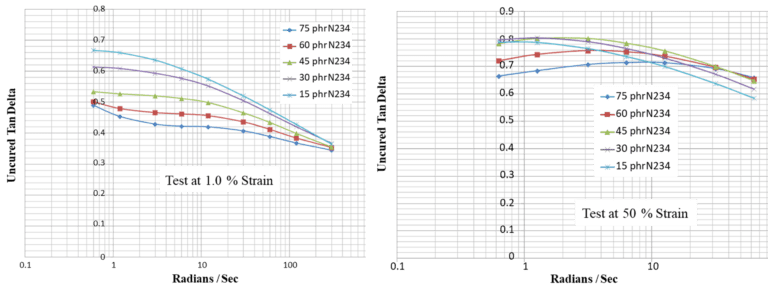
Figure 4 Results of increasing concentration of filler on uncured Tan Delta at 1.0% and 50%
Faster. Easier. More Repeatable. What's Not to Like?
While a capillary rheometer, such as the ARC 2020 is the most common and accurate way to predict die swell, it can be difficult to use. This complexity can result in unintentional variability of data, if not managed by a skilled operator.
On the other hand, the Premier RPA provides these advantages:
- Faster and more productive prediction of extrusion die swell.
- Simplicity of operation.
- Repeatability is better with the RPA to measure rheological properties relating to die swell than with the Capillary Rheometer.
- Applicable to routine QC to provide early characterization of batches prior to processing, reducing the costs of scrap, downtime or rework.
The right instrument for a swell job.
The Premier RPA is specifically designed to measure viscoelastic properties of elastomers and rubber compounds. These properties are the key parameters for the understanding of polymeric flow. Premier RPA can effectively predict the die swell of rubber compounds in extrusion processing, with excellent correlation between die swell and uncured compound viscoelastic data (Tan δ) measured under frequency sweep. In setting up your test, the specific strain amplitude applied during the performance of the RPA frequency sweep is very important. Increasing the applied strain in a sequence of multiple frequency sweeps can measure an uncured tan δ inversion. Actual process conditions, screw speed and temperature, head temperature etc., can also be considered as important setting reference parameters.