Finding Balance: Measure Cure & Blowing Reactions Using an RPA
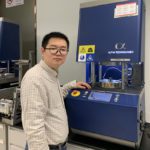
Author
Li Wan
Application Engineer, China
Whether you are extruding or injection molding, the production of foaming or blowing compounds can be a tricky business. The vulcanization of sponge rubber products requires a delicate balance between two separate chemical reactions within a single cure cycle. The blowing agent reaction must take place at the appropriate point relative to the vulcanization reaction to assure you get the desired cell structure in the finished part. If the blowing reaction is too early, the cells may burst and you can end up with a very large open cell foam with poor physicals. If the blowing reaction is too late, you may not get any expansion at all – the cells may not form or be too small. This process is demonstrated in Figure 1 below. It is very important to control and balance these two reactions to obtain the desired sponge rubber properties. To quantify this Blow-Cure balance, you must be able to measure and analyze both the cure reaction and the blowing reaction simultaneously. Moreover, most uncured sponge rubber compounds have relatively low viscosity. Therefore, an optimal test for the proper blow-cure balance of a sponge rubber compound must measure both reactions and viscosity precisely.
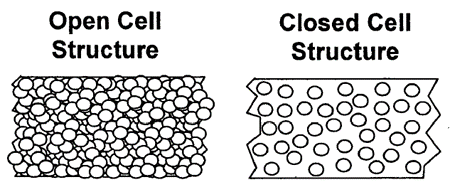
Figure 1 Sponge Rubber Compound Chemical Reactions at Curing Process
Alpha’s Premier Rubber Process Analyzer (RPA) has been readily accepted by the rubber industry for routine testing of rubber compounds. By adding a standard torque and pressure 2-in-1 transducer on the upper die, you are able to measure the torque as well as the cavity pressure simultaneously. In this post, we’ll show you a more efficient way to measure cure & blowing reactions.
But First, A Bit of Backstory on Blow and Cure
Cellular rubber products have been produced for over forty years, thanks to the invention of methods to activate organic blowing agents. Today, cellular rubber products include weather stripping, seals, gaskets, cushion materials, footwear soles, thermal insulation, toys, foam mattresses and more. To achieve a cured cellular structure a rubber compound will contain certain organic or inorganic chemicals known as blowing agents. At the curing temperature these blowing agents decompose and produces a gas to generate cellular structure. At cure temperature, both a cure crosslinking reaction and a blowing agent decomposition reaction happens at approximately the same time.
Typically, inorganic blowing agents result in open cell structures, while organic blowing agents produce closed cell structures. In open cell structures cells are interconnected and readily absorb water, as with a sponge. Close cell structures have isolated cells where the gas from the blowing agent is encapsulated. Closed cell structures can impart excellent thermal insulation characteristics and sound absorption properties.
In addition to cell structure, the size and concentration of the cells is also important to the final properties of the material. The concentration of the cells, known as the blown cellular density, can affect the material’s compression-deflection, or the amount of force needed to compress a specific area of foam.
In the past, testing the blowing reaction was performed on a Moveable Die Rheometer (MDR), but with the limitations of that instrument. Otherwise blowing agents were incorporated into the compound and processed based on experience. As experienced quality and manufacturing managers continue to retire, the experience factor is rapidly disappearing from the factory. You really need an RPA to get the precise sensitivity you need to accurately measure blow and cure reactions.
The Science of Balancing Cure and Blow Reactions
According to Boyle’s Law, the number of gas molecules formed during blowing reaction relates directly to measured pressure in closed die cavity. This relationship is expressed by the following equation.
P * V = n * R * T
Where P is the pressure, V is the Volume, n is the number of the gas molecules, R is the universal gas constant, and T is the absolute temperature. In other words, you can measure the blow reactions through measurement of pressure changes.
To properly measure the pressure buildup during the decomposition of the blowing agent in the compound, the instrument must hold the test specimen under low cavity pressure. If the cavity pressure is too high, gas pressure generated by the compound cannot be measured. Typically, while fully-filled cavity pressure is best for measuring rheological properties before and after cure such as viscosity, it is also much higher than the pressures generated by blowing agent reactions. In addition, some blowing reactions can have side reactions that inhibit the main reaction and can be exacerbated in a high-pressure environment. And lastly, this approach does not closely replicate the factory process.
So, to reduce initial cavity pressure and allow blowing reaction measurement, the cavity is partially filled, as shown in Figure 2. The partially filled cavity method is a good compromise in which there is enough rubber sample to measure the torque changes, but also enough free volume to measure the pressure buildup from the decomposition of blowing agents in the rubber compound.
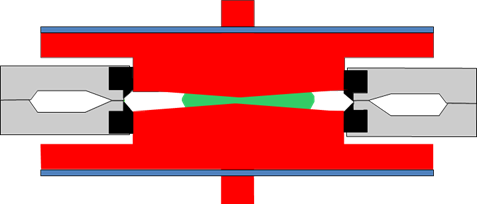
Figure 2 Diagram of partial filled sealed test cavity
The fill factor changes depending on the nature of the sponge compound being tested. You need to carry out pressure measurement of different sample weights to determine the optimal fill factor. The ideal sample mass will be one that creates the highest delta pressure and shows the smallest amount of change between masses.
As can be seen in Figure 3, the sample weight at maximum Max-Min has the best sensitivity to blowing reaction. If the sample weight exceeds optimal fill factor, the pressure measurement could be restrained, and the true gas amount cannot be detected. If it is lower than optimal fill factor, the sensitivity would be poor. And the sample weight variation should be controlled to a tolerance range of ±0.01g to get good precision. In addition, samples cut in a uniform circular shape produces repeatable test results for both torque and pressure responses.
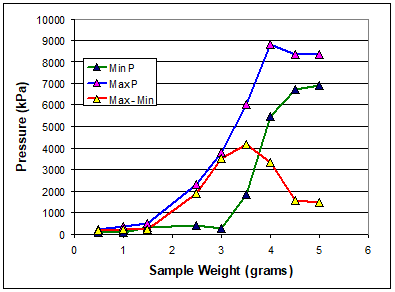
Figure 3 Effect of Sample Weight on Pressure
Figure 4 shows the test curves of the sponge rubber compound. Like the vulcanization torque curve, the data points to judge blowing reaction include the minimum pressure Pmin, the maximum pressure Pmax, the maximum pressure rate, and the difference between Pmax and Pmin which relates to the blowing agent decomposing gas molecules number. The actual pressure and torque curve shape could vary for different sponge rubber compounds. The blowing reaction starts earlier or later than cure reaction, which would get different “bubble cell” structures. The cure percent at Pmin when blowing agent start decomposing, and the cure percent at the maximum pressure rate are the key data points to analyze the cure & blowing reaction balance.
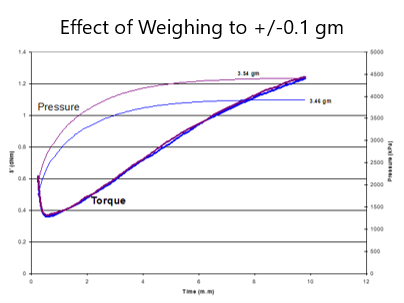
Figure 4 Test curves of the sponge rubber compound.
Figure 4 relates to the blowing agent decomposing gas molecules number. The actual pressure and torque curve shape could vary for different sponge rubber compounds. The blowing reaction starts earlier or later than cure reaction, which would get different “bubble cell” structures. The cure percent at Pmin when blowing agent start decomposing, and the cure percent at the maximum pressure rate are the key data points to analyze the cure & blowing reaction balance.
Faster. Easier. More Accurate Measurement of Blowing Reaction
It is widely known that Premier RPA has proven its capabilities in measuring the reaction kinetics of rubber vulcanization. Somewhat lesser known is the fact that you can also carry out precise measurement of blowing reaction kinetics using the RPA. From the pressure curve, the time to reach a percentage of the blowing reaction may be calculated in the same manner as it used to calculate the time to a percent cure in the vulcanization reaction. The Arrhenius and Van ’t Hoff equations are still available for the study of blowing reaction kinetics – activation energy can be calculated and differences in sponge formation at different temperatures can be predicted. Usually, the blowing reactions tend to have higher activation energy than many cure systems, that’s why the Blow-Cure balance changed with the cure temperature selection. This capability enables a better understanding of the interaction between blowing and curing, also provides a precise method for balancing both.
Benefits of Using an RPA for Measuring Blow and Cure Reactions
- Faster and more productive measurement of the balance of cure and blow reactions.
- Measurement of rheological properties and pressure in one test.
- Simplicity of operation. The RPA user friendliness enables testing to be easily performed, and the sample preparation step is only about sample weighing.
- Excellent sensitivity. By increased frequency (data rate), controlled strain or controlled stress tests and improved low torque sensitivity with soft materials, RPA has a better test sensitivity than other instruments.
Getting to a Better Balance
Premier RPA is capable of precise and sensitive measurement of both the pressure and vulcanization reactions of a sponge rubber compound. The RPA die system is uniquely suited to measure both reactions in one test because the test cavity is sealed, and the dies have large radial grooves to maintain contact with the sample, the combination of strains and frequencies can be set freely to meet the requirements of different types of sponge compounds. By precise control of test sample volume, both vulcanization changes and pressure changes can be accurately measured in a single test. Reaction kinetics analysis also gives you a precise method for balancing the blowing and curing process. These capabilities could help you design your sponge rubber formulations more precisely and efficiently.