Inventing the Rubber Process Analyzer
A Long and Winding Road
The Rubber Process Analyzer – the RPA – has had a rather complicated history. It began as an R&D project at Monsanto Instruments & Engineering, a division of Monsanto Rubber Chemicals, to build on the success of their invention of the Moving Die Rheometer (MDR). However, like the invention of the MDR before it, the RPA took a series of zigs and zags before becoming a successful and valuable instrument for the rubber industry. That should not be surprising. In any R&D project, the path is not usually straight. Sometimes you stumble off the path and end up in a ditch. (Or maybe you stumble into what you think is a ditch only to discover a secret underground passageway that gets you closer to where you’re going.)
To really put the invention of the RPA into perspective, it’s necessary to understand the two generations of instruments that came before it, and how moments of alternating successes and failures – sort of like sine waves – finally resulted in a reliable, repeatable, reproducible resource for rubber and polymer manufacturers.
How the Oscillating Disc Rheometer changed the rubber industry.

The rubber industry is not keen on making changes. The patent for the Banbury Mixer was awarded in 1916 and it is still in use today, with a minimum of modifications and new features. The Mooney Viscometer arrived in the 1930s and is still found in rubber factories worldwide. The Mooney provided data on the onset of vulcanization (scorch) and a crude indication of average molecular weight, but you couldn’t really see the ultimate state of cure.
It wasn’t until the 1960s and ‘70s that scientific instrument companies began developing and commercializing rubber cure testing methods using die systems. BF Goodrich introduced an instrument with a cone configuration. Goettfert, in Germany, developed an unsealed rotor-less die method, but with limited success in providing cure test data. But it was Monsanto Instruments & Equipment that provided a major breakthrough in cure technology with the invention of the Oscillating Disc Rheometer (ODR). The patented ODR system, known as the R100, had the only sealed and pressurized sample chamber, which is important for the collection of good repeatable data. It quickly became the industry standard around the world.
The instrument fits on a tabletop or counter in a lab. The data collection method was a flatbed chart recorder. The ODR was operated at 1, 3 or 5 degrees of arc, although statistical analysis showed that 1 degree provided the best signal-to-noise sensitivity and produced the best data.
Henry Pawlowski, rheology fellow at Alpha Technologies (formerly Monsanto I&E) recalls, “The big breakthrough that the ODR brought to the rubber industry was that it was actually three tests in one. Other instruments tended to provide data for one item and only one item. But the ODR could provide three pieces of data that the rubber industry wanted. They got processing information – the properties of the material before cure, including an estimate of the molding time required. You could get cure data – how fast does it cure. And you would get a maximum property state of the material – what the final properties are going to look like.”
The ODR provided tasks that were otherwise difficult to do. And suddenly, companies would test every single batch, because it was a relatively fast test to do for quality control purposes. It was also popular for evaluating new compound formulations in the R&D lab.
There were, of course, problems and limitations of the ODR. The rotor was unheated, so tests were not under true isothermal conditions. Seal and bearing friction added signal to the measurements that did not come from the rubber sample. Changing test temperature could take up to an hour. And removing the embedded rubber sample from the rotor was a major pain – often requiring removing the rotor from the machine to be able to pry the sample off.
Still, even a flawed instrument can be worth using if you have reasonably good sensitivity and good repeatability. The ODR became the workhorse curemeter for the industry.
One step forward, two steps back… the invention of the Moving Die Rheometer.

Meanwhile, the discussion at Monsanto I&E was whether or not to develop the next generation curemeter. Would the new curemeter cannibalize sales from the ODR? How would customers react to a new instrument that shifted the data, even if the data was more accurate? With the ODR already established why would anyone bother to buy a different curemeter?
In the end, the decision was made to proceed on the basis of, “If we don’t do it, somebody else will.”
And so, the project went forward to create a Moving Die Rheometer, to be known as the Classic MDR. It produced a number of breakthroughs in design and engineering. Probably the most challenging and complicated issue to resolve was the design of the upper seal. Another critical issue that was solved was how to calibrate torque. But as Henry Pawlowski remembers, “I spent five years trying to help the engineers develop the MDR. And when we were done, and introduced it, it was a dismal failure.”
One of the problems was the “fenced” die that had been patented by Monsanto I&E, with rings on the upper and lower dies that were engineered to intermesh. “The thinking was that the design created more signal,” recalls Pawlowski. “In addition, the rotor was eliminated, and all elements were heated. It was only later, as we got smarter, that we discovered the fences did not have uniform temperatures, so it was not a true isothermal cure test. What’s more, the fences were a great place for slippage to start. But it was our patent, and we were going to make the most of it.”
There were about six Classic MDRs (Moving Die Rheometer) sold. One customer in Germany bought two and immediately had trouble getting good reproducibility between the instruments. Henry Pawlowski was dispatched to the customer’s factory and spent three weeks in Cologne running tests. He saw the problems and began working on a different die system.
One of the rubber compounds that was used to evaluate the instrument had a bonding agent in it. And if you ran enough tests eventually it would bond itself to the fenced dies. Pawlowski’s concept was to simplify the die set completely, using a biconical design with no grooves or bits or fences in the center.
At that time, Monsanto I&E manufactured all its components in-house. They had a mechanical engineer named Les Randall who was also a machinist. Whenever Henry Pawlowski or another engineer would say, “Hey, I want to try this out,” Les would look at it, make some quick drawings and in a day or so it would be ready for testing. As a result, the design team could accelerate their progress.
Once the simpler design was incorporated, the MDR started looking more like the MDR of today. Issues involving the seals and the torque calibration spring were resolved.
Jeff Ward had joined Monsanto in the mid-1980s as a field service engineer just as the Classic MDR was introduced. He saw the problems it was causing in the field and contributed that knowledge to the team developing what was to become the Series 2000 MDR.
“When we came out with Series 2000, the MDR was revolutionary. Nobody saw it coming,” says Jeff Ward. “We had to convince customers to go from an R100 to our new MDR – but the data was totally different. We had to show them, ‘hey… this is the future.’
Tire companies saw that correlating the data on the MDR 2000 with their R100 would take running the same rubber on both machines. In six months or less they will have their new specs. “And once they finished that correlation,” recalls Ward, “they were off and running.”
And now the movie… the invention of the RPA.
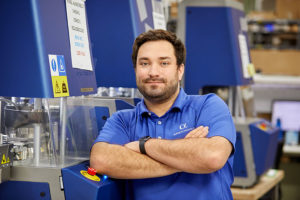

In 1975, because of oil price surges and shortages, Congress created the Corporate Average Fuel Economy or CAFÉ standards. The car companies first began working on the obvious – reducing weight, improving motor efficiency. But, along the way they discovered that the rolling resistance of a car’s tires made a big, big difference on fuel mileage. Their focus turned to the tire manufacturers.
The car companies informed tire companies that they were going to establish a specification for rolling resistance. And, by the way, “if you fail to meet it, we will be forced to reject your tires.” The problem: how can you determine the rolling resistance of a tire before you build the tire?
Goodyear tackled the problem using the Rheometrics System IV – a dynamic mechanical analyzer – to determine correlations to rolling resistance. However, System IV was expensive and required a highly trained technician to run the tests. It was not a good solution for the production floor.
Goodyear had been an early adopter of the MDR 2000. Now they began working with Monsanto I&E on the development of a new instrument – a Rubber Process Analyzer, or RPA.
“The very first designs for the RPA had a lot of issues where the concept didn’t play well with reality,” recalls Jeff Ward. “It was a very interesting, very complicated design. The die assembly had little fins that stuck out. It was revolutionary as far as anything we had seen before. But we learned a lot from that. It was the stepping-stone to get where we needed to go.”
The design took an MDR 2000 and changed the motor to allow it to operate at different speeds. The new instrument was named the MDR-P – the P stood for Processability. You could change the frequency of oscillation, but you could not change the strain.
This device was sent to Goodyear, who spent a year doing evaluations and tests. When they were done, they presented their conclusions. They said, “We cannot have an instrument that just varies frequency. We must have the ability to vary strain, as well.” And Monsanto I&E’s design and engineering teams went to work to meet Goodyear’s expectations.
“Frequency is easy – there are a lot of motors that can run at different speeds and change the frequency of oscillation,” notes Henry Pawlowski. “But changing the strain was more complicated. The first effort to make the RPA with strain variability utilized a little motorized eccentric. But after it was finished, we determined it was a horrible design because of the slop (hysteresis) in the system. It was something you’d really notice when you went to low strains. The percent error was very high, so you didn’t get repeatable data, you didn’t get reproducible data, you were in a lot of trouble.”
It was decided that changing to a direct drive motor was the best solution. The engineers found a motor made for robotics that had 500,000 points of resolution per 360 degrees of arc, allowing the motor to move at angles as small as 0.05 degrees (0.7%).
The computer that would operate the RPA, was a critical element in getting it to work. The original operating system that was used was developed by IBM known as OS/2. When the test was done the software would produce data files that were compatible with Microsoft Excel – one file for each subtest which were then analyzed using Excel Macros. Results could be read on the latest dot-matrix printer.
Version 1 of the software provided isothermal cure, frequency sweeps and strain sweeps, however the number of raw data points was limited to about 250 data rows in Excel. Version 2 introduced a Variable Temperature Analysis (VTA) subtest that allowed non-isothermal cures. Version 3 introduced the stress relaxation subtest.
John Dick, rheology fellow, joined Alpha Technologies just as the RPA went into beta testing. “The die design of the RPA was virtually identical to the die design of the MDR,” he recalls. “The difference between them was frequency, strain and temperature. You could change the temperature more quickly with the RPA than you could with the MDR, especially cooling down because you had forced air cooling. The RPA had a direct drive system that oscillates back and forth sinusoidally and can change strain very quickly, so you could start from low strain and work your way up. The frequency was always 100 cycles per minute for the MDR, which was a carry-over from the ODR. But with the RPA we could vary the frequency to be what we want.”
With the successful implementation of strain sweeps, along with breakthroughs made during the development of MDR 2000 – such as biconical die design, die gap adjustment, better temperature accuracy and recovery, high performance seals, and the first sample automation system – Monsanto I&E sent five beta versions of the RPA to customers for their evaluation.
“Goodyear really fast-tracked the development of the RPA,” notes Henry Pawlowski. “They knew how it had to function and they knew what the results should look like.”
Monsanto I&E rheologists ran comparisons with scientific rheometers like System IV and found that the correlations were incredibly good. Comparisons were also made to data for stress relaxation of uncured materials on a Mooney Viscometer. The RPA produced good data that correlated well with the Mooney. ” The big idea was that the RPA could be a dynamic tester that could be used in a production environment and produce data close to what a scientific rheometer would produce,” says Henry Pawlowski.
During 1991 and 1992 engineers continued to come up with solutions to problems in the RPA’s design. The seals used in the MDR were also put into the RPA but were utterly destroyed in a short period of time, especially at high frequencies and high strains. A new, stronger polymer was incorporated into the design. The need for cooling was obvious when trying to reduce the temperature during a test with closed dies. A series of experiments were conducted that resulted in a straightforward design that rapidly brought the air into the cooling area and allowed it to exit.
Monsanto’s automation system using film, which was first developed for the R100, provided easy sample removal, but produced more slippage. Different films were investigated until the team found a nylon film that provided resistance to slippage similar to no film. Further work was done at the request of Bridgestone to provide an alternate film that would still give good data performance even up to 100% strain.
But one more formidable challenge remained.
Previously, scientific rheology instruments such as the System IV used an Open Cavity system. But when you went to high strains the sample would start falling apart, because it was not constrained. When that happens, the signal coming from the rheometer becomes very, very noisy. This noise is referred to as Edge Effects: on the inside you can get great flow and movement, but on the outside it’s not good data.
“One of the things that the RPA introduced was a system that eliminates or significantly reduces Edge Effects,” says Henry Pawlowski. “Because when you have everything sealed up, when the lower die moves the sample cannot go anywhere. And when you run the high strains, you get what’s known as a square wave and you can do a Fourier Transform to that signal and the harmonics tell you something about the molecular nature of the material.”
“The RPA brought us into the realm of science, rather than the realm of tradecraft. Tradecraft is when you can’t put numbers on things, so you have subjective words to describe things… whether it’s a ‘smooth’ extrusion or ‘seems a little tacky today,” says John Dick. “While the MDR moved us down that path because it allows us to see the ultimate state of cure, the RPA can go much, much further. We can tell you how this material is going to process. We can tell you the excessive die swell in extrusion operations – are you going to have non-fills in a certain mold filling operation. All this can be determined from the tests we have now, which were not available by measuring with crude instruments such as the Mooney.”
“We were able to simulate everything that rubber goes through in a production line – mixing through extruding or putting it into a mold,” says Jeff Ward. And that was the key – that’s why they called it the Processability Tester. The RPA was able to check the process from the mixing end all the way through to the molding into the final product and be able to cool it back down and test it at whatever temperature the rubber was going to operate at. All of that had never been done before.”
By 1992 the RPA 2000 was finally ready for prime time.
It ain’t over until we say it’s over!
Alpha’s RPA was hailed as a “Ferrari” of an instrument when it was introduced. It gained rapid acceptance for its ability to test a compound before, during and after cure. But there was still work to be done, including development of tests and standards to guide customers in the use of this innovative technology.
And while Henry Pawlowski was the pit crew engineer behind building it, John Dick became the driver. Over the last 30 years, John has continually developed tests and correlations that help rubber and polymer manufacturers get more value out of their materials.
“The challenge was… the RPA gives you a lot of information, but does it give you knowledge?” notes John Dick. “I was trying to convert the information into knowledge that rubber technologists could use in solving a variety of problems.
“In a factory setting you must make fast decisions. If something is going wrong, you want to know about it and understand what the corrective action would be. So, I worked a lot in those sorts of situations, trying to allow customers to interpret what the RPA is telling them and take corrective action,” he says. “Since then, I’ve documented several ASTM (American Society for Testing and Materials) standard methods using the RPA. They deal with processability, they deal with measuring cured physical properties and what sort of correlation you can get with traditional tests. Some of these tests are short – It only takes about 4 minutes to run the whole thing. But that’s what you want in a factory – you want something quick and to the point.”
Between 1992 and the introduction of Premier RPA in 2018, the instrument underwent continuous improvement and innovation. “Comparing what we can do today with the RPA is light years ahead of what we could do in 1991,” says John Dick.
“We put a better motor in our Ferrari,” recalls Henry Pawlowski. “The original motor of the RPA was able to do 500,000 counts in 90 degrees. The new motors can do 1,000,000 . And there’s a concept called oversampling, and that allows you to get to lower signal levels. What that means is that instead of using 16 data points like an MDR, or even 120 like the original RPA, now you can use over 1,024 data points and get to an even lower signal level.”
“We learned how to improve our signal-to-noise ratio on very low strain testing,” says John Dick. “That’s critical because of all the silicas being used today. In the old days we hardly used any silica because it was hard to mix. But Michelin received a patent that if you used a heavy load of silica and got it effectively dispersed, then you got better rolling resistance. That’s why we’re doing sub-ambient now – because it’s the only way to determine silica silanization. We’re the only ones I know who make an RPA that can go that low in temperature, and accurately measure Tangent Delta at 0 degrees C.”
The old OS/2 platform gave way to Windows and its successive generations before being ported over to Eclipse – software developed in the Netherlands. Eclipse was bought by Alpha Technologies in 1999 and a team of software engineers relocated to Akron, Ohio to develop Alpha’s Enterprise platform. “One of the things we started doing was replacing the Windows software that originally went with the RPA,” says Peter Boogaard, software engineering manager, Alpha Technologies since 1986. “The design of Enterprise was to have a computer to talk to the instrument through a program called Workbench. And then we have a management program that defines the tests, defines the materials, defines the specs. And we developed a web application that we call the Online Manager.”
And the beat goes on.

The ability to measure at such a low strain so accurately was a great breakthrough for the RPA. But other improvements such as Precision Dynamic Modulus (PDM) were developed and added to Premier RPA. Sub-Zero™ technology is providing greater insight into performance characteristics like traction in wet and icy conditions.
Alpha has continued to expand the knowledge base of RPA tests and correlations through their work on ASTM and other global standards committees. “But one thing I observed was, when you create something that’s never been available in the world before, as companies run tests and collect data and make all sorts of discoveries, the more discoveries they make the less they tell you, “Says Henry Pawlowski.
“That’s why I wrote so many books and documented so many standards,” says John Dick. “I’m trying to share the science of it. On the other hand, a standard tends to make a technology permanent.”
After 30 years, the RPA is proven technology for the rubber and polymer industries. If the Banbury Mixer and Mooney Viscometer are any indications, the RPA will be in use through the end of the century. As you know the rubber industry is generally not keen on making changes.
Have You Heard?
We're looking for the Oldest RPA Still in Service
Alpha instruments have always had a reputation for long-lasting service. (The average age of the MDRs at one company is 26 years!) Alpha is currently looking for the oldest RPA still in service and is sponsoring a sweepstakes to find it.
Alpha’s Oldest RPA Sweepstakes is open to anyone who has an Alpha RPA in service. The winner of the Oldest Alpha RPA prize will be determined by the serial number on the machine. The winner of the Sweepstakes prize will be determined by a random drawing of all eligible entries.
Related Links
Webinar: The Future of Thermoset Testing
The Future of Thermoset Testing: A Look at the Latest...
Read MoreApp Note: Predicting Low Temperature Compression Sets
Predicting Low Temperature Compression Set with a Rubber Process Analyzer...
Read MoreWebinar: Reduce Raw Material Variation
Webinar: Reduce Raw Material Variation Using Rheometry Learn From The...
Read More